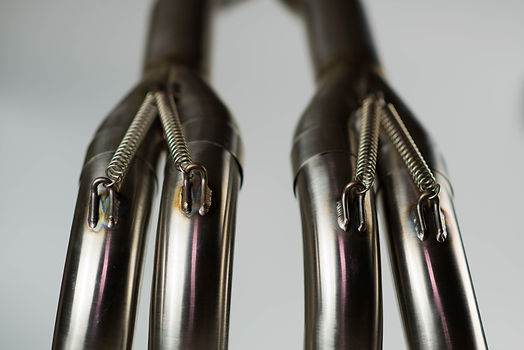
Fabrication & Welding
Fabrication and welding are the basis of our manufacturing process at GoodFabs.
We TIG weld thin-wall stainless steel and nickel alloys, such as inconel, the material with which we work most.
With such a scarce labour resource available to us, we have to make sure that our manufacturing processes are well-planned and efficient.

Fabrication
Most of our fabrication at GoodFabs involves lightweight exotic metals which perform well in high heat environments.
Nickel alloys such as inconel are not readily available in tube form so we start the fabrication process with flat sheets of metal with a material thickness that typically ranges from 0.5mm to 1.6mm.
Large thin sheets are precision cut with a guillotine and then rolled and seam welded to form a custom-made tube.
This tube is then mandrel bent on one of our Clark & Lewis tube benders using a range of custom-made bend tooling that is probably the most extensive outside the aerospace industry.
A set of perfectly formed bends is then passed onto the fabricator/ welder who will have been provided with a CAD drawing, a fabrication jig and a set of laser cut and machined components which he will use to make the part or exhaust system.
Our skilled fabricators will discuss the precise order and method of manufacture with the management team to ensure that the most efficient manufacturing approach is used, taking into account any other post-fabrication processes, such as heat treatment or shot peening, that may be needed either during or post-fabrication welding.
Once an exhaust part has been completed it will be passed onto our separate inspection department where it can be CMM inspected using our FARO arm or laser scanned, taking into account the tolerances prescribed by the customer.
The part may also go through an in-house NDT process using dye penetrant to confirm the quality of the welds.
Other post fabrication processes, such as shot peening or heat treatment may then be carried out before being returned for a final inspection.
Parts can be marked by laser etching and carefully packed for same day or overnight delivery.

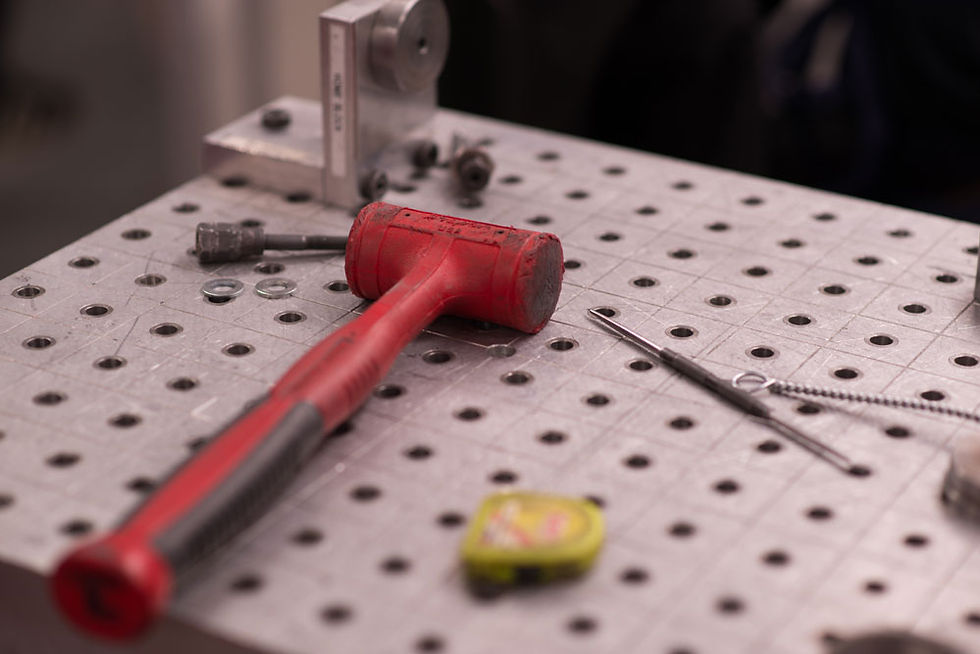

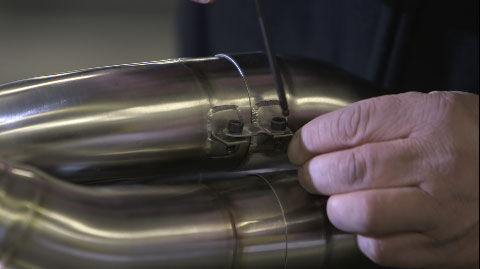

Welding
The TIG welding process mainly refers to Gas Tungsten Arc Welding (GTAW).
TIG welding requires only three components: heat, shielding and filler material.
The heat is created by an electric current passing through the tungsten and arcing to the metal to be welded. This forms a ‘puddle’ of molten metal where the filler material can be dipped in by hand.
The shield is created by a protective gas flow around the heat affected zone, effectively reducing the risks of contaminating the metal with atmospherical elements.
The ability to soft start and stop the heat makes the TIG welding process an ideal process to weld thin-walled material. With metals being as thin as 0.3mm, the slightest gap or mistake can cause a hole or large inconsistencies in the welds.
At GoodFabs, we closely monitor the weld quality in our inspection department which can perform a detailed NDT inspection.
Another large advantage of TIG welding is the uncleaned finish; a good TIG weld is so clean that it does not require any cleaning up or grinding to smooth it out, making it ideal to weld thin walled exhaust systems where the exhaust gasses flow at high speeds and any inconsistency might reduce the power output of the engine.
Welding thin walled exotic materials such as inconel, titanium or even stainless steel and aluminium requires a perfect fit and very good welders.


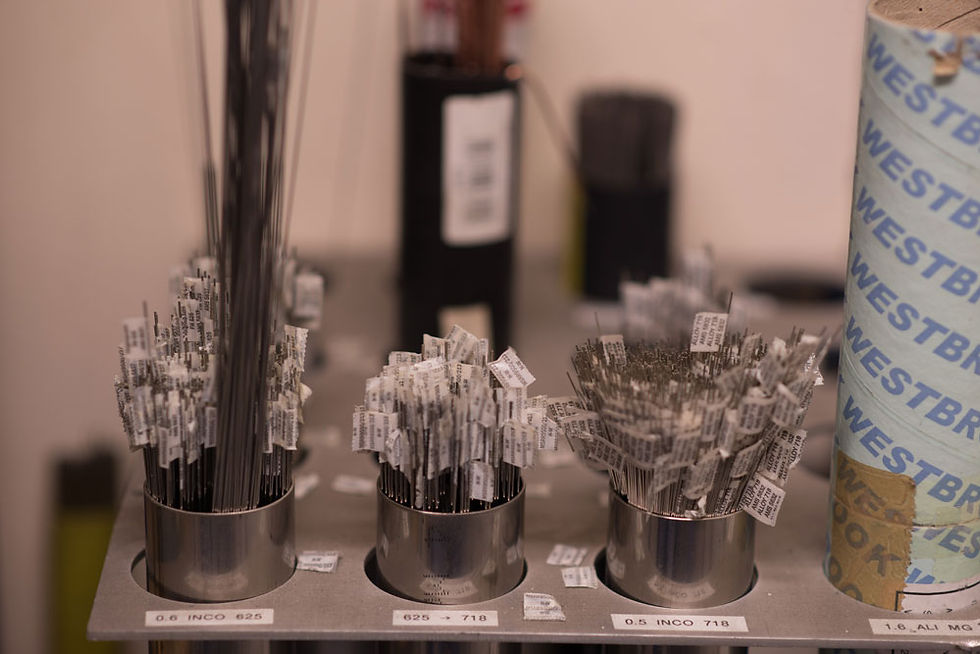
